Researchers develop the missing component in robotic textiles
04 Apr 2023 Anna Demming
Wearable fluidic systems The fibre pump can be seamlessly woven into textiles. (Courtesy: © LMTS EPFL)
For years the snag with soft robotics has been that a lot of it requires some kind of pump that, until now, has only been available in more conventional un-wearable forms. Sensors, actuators, as well as energy storage and generation devices, have all been developed in the form of soft fibres that can be woven seamlessly into clothing. However, the soft pumps that have been developed lack the fluidic power to make them really useful, and have not been made as fibres.
Reporting their findings in Science, Michael Smith, Vito Cacucciolo and Herbert Shea at École Polytechnique Fédérale de Lausanne (EPFL) in Switzerland have developed a soft hydraulic pump that not only beats the fluidic power previously achieved by a factor of ten but also takes the form of a fibre.
“Hydraulic actuating is interesting because it’s soft and compliant, and you can put it on the body,” says Shea. He and his colleagues had been largely motivated by long-term goals to develop a soft comfortable exoskeleton that someone could wear for rehabilitation or strength support, for instance, or to enable someone with limited mobility to walk.
The fibre pump operates based on electrohydrodynamics, a principle it shares with a stretchy pump that Shea’s group demonstrated in 2019. Whereas that pump had electrodes that alternated along the inside of a fluid-filled channel like interlaced fingers, the fibre pump contains positive and negative electrodes coiled around the inside of a fluid-filled tube. The potential difference between the electrodes ionizes molecules in the fluid and accelerates them up the tube. As surrounding molecules get caught up with the ionized molecules, the fluid shifts up the tube generating pressure.
The mechanism of the pump relies on the electrodes being held in place on the inside of the tube such that there is direct contact between them and the fluid so they can inject charge into it. While challenging, the researchers found a natty route to the required geometry by twisting the tube material and electrodes together around a mandrel.
“Any metric you can think of to measure a pump gets better when you make it into a fibre by a factor of at least 10,” says Smith, who developed the coiling geometry, citing improvements in pressure, flow rate, efficiency and power. This is largely thanks to the continuous pumping along the tube that the helical structure gives, which leads to smoother fluid flow, Shea explains.
The cylindrical symmetry also lowers the fluidic impedance, while the wires may also provide a more ionizing field distribution than flat electrodes. The leap in fluidic power delivered by the device came as a welcome surprise to the researchers, since – as Smith points out – the pump is very difficult to simulate accurately due to all the “coupled physics” involved.
A haptic sensation
The pump is still a little way from the efficiency required for a soft exoskeleton, but the researchers have demonstrated how effective it can be for generating haptic stimuli – the sensation of touching an object. The buzzing feeling of typing on a touch screen is an everyday example of tactile haptics, but, as Shea points out, “a lot of how we perceive the world is actually thermal conductivity.” In a virtual world, recreating these thermal experiences can improve the sense of immersion, but it has been difficult to implement. The fibre pumps can locally circulate chilled fluid, creating local thermal haptic stimuli without needing a huge array of separate pumps and valves.
Heat management with a thermal haptic glove
Real-time thermal imaging of the glove as individual fibre pumps are activated one by one. Courtesy: © LMTS EPFL
Play Video
Jun Zou is a professor at the State Key Lab of Fluid Power and Mechatronic Systems in China who has also worked on soft pumps. Although not involved in this research, he describes it as “an effective integration of actuation and stitchability for wearable applications”.
Andrew Conn, an expert in soft robotics at the University of Bristol in the UK, who was also not involved, describes the work as “an exciting step” towards comfortable wearable technologies for physical assistance and thermal regulation. He highlights the simple fabrication method, which can scale up the length of fibre pump produced. “This should help to translate this technology out of the laboratory and into practical wearable applications much more quickly,” he adds, although he also points out that the large electric fields and specialized pumped fluid may be limitations of the current design.READ MORE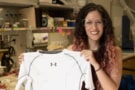
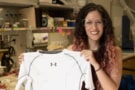
“We do operate at a high voltage, but the power consumption of the pumps is very modest,” says Smith in response. He adds that the fibre pumps can be battery powered and carry a current well below any safety thresholds for human interaction.
The researchers have demonstrated that the fibre pumps can apply the pressure needed to actuate artificial muscles, render thermal haptic stimuli in gloves and create active cooling garments. In the future they hope to broaden the selection of liquids they use, but they are now primarily looking at ways to improve the efficiency of the fibre pumps, make them longer, and interweave them with other active fibres such as sensors and actuators, to maybe one day produce a soft and comfortable exoskeleton.
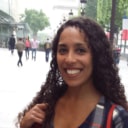
Anna Demming is a science journalist based in Bristol, UK
FROM PHYSICSWORLD.COM 12/5/2023
Δεν υπάρχουν σχόλια:
Δημοσίευση σχολίου