Laser ‘speed limit’ leaves defects in 3D-printed parts
10 Dec 2020 Isabelle Dumé
3D printing techniques are transforming many areas of manufacturing. One such technique, laser powder bed fusion (LPBF), is particularly attractive because it can be used to make complex metal parts that would be difficult or impossible to manufacture conventionally. However, it suffers from a major drawback in the form of tiny voids that weaken and degrade the metal. Researchers in the US and China have now identified how these voids are generated, and how they become trapped as the metal solidifies – findings that could help manufacturers find ways to control them, and thereby improve 3D metal-printing processes.
In LPBF, a high-power laser, guided by a digital computer-aided design and drafting model, is scanned across a thin layer of metal powder. The heat from the laser melts the metal powder in localized regions and fuses it to the layer of metal directly underneath. While this process is highly versatile and fairly speedy, the objects it creates are often riddled with microscopic, vapour-filled pores that drastically limit the material’s toughness and fatigue resistance.
“Keyhole” structures
When a high-power laser boils molten metal, it often generates deep and narrow gaps. These gaps are known as keyholes, and it had long been suspected that they were related to defects in the finished 3D-printed part. The exact relationship between keyholes and porosity was not, however, fully understood.
Researchers led by Anthony Rollett of Carnegie Mellon University, Tao Sun of the University of Virginia and Cang Zhao of Tsinghua University have now used high-energy X-rays derived from the Argonne National Laboratory’s Advanced Photon Source to image how keyholes and pores form in a titanium alloy (Ti-6l-4V) during LPBF. Among their observations was that keyholes can change shape during the process. In particular, the tip of the structure can morph into a “J” shape and pinch itself off, leaving a large bubble behind.
If this bubble never reconnects to the main keyhole, Rollett explains that it can instead collapse, generating an acoustic shock wave as it does so. This shock wave pushes the remaining pores away from the keyhole, thereby ensuring that they survive long enough to become trapped in the re-solidifying metal.
Despite the role that keyholes play in creating voids, Rollett and colleagues emphasize that keyholes themselves are not flaws. In fact, they have a positive role to play in LPBF, as they increase the efficiency of the laser: once inside a keyhole, the beam undergoes multiple reflections that enhance laser light absorption. It is only under certain conditions that the keyhole changes shape and becomes unstable, generating unwanted pores in the process.
Stay out of the “danger zone”
To find out what these conditions are, the researchers studied how the speed at which the laser is scanned over the metal power relates to keyhole instability. They found that keyholes become more unstable if the laser is scanned too slowly across the metal powder. Such slow scanning speeds increase the laser’s power in a localized region, allowing the metal there to overheat.READ MORE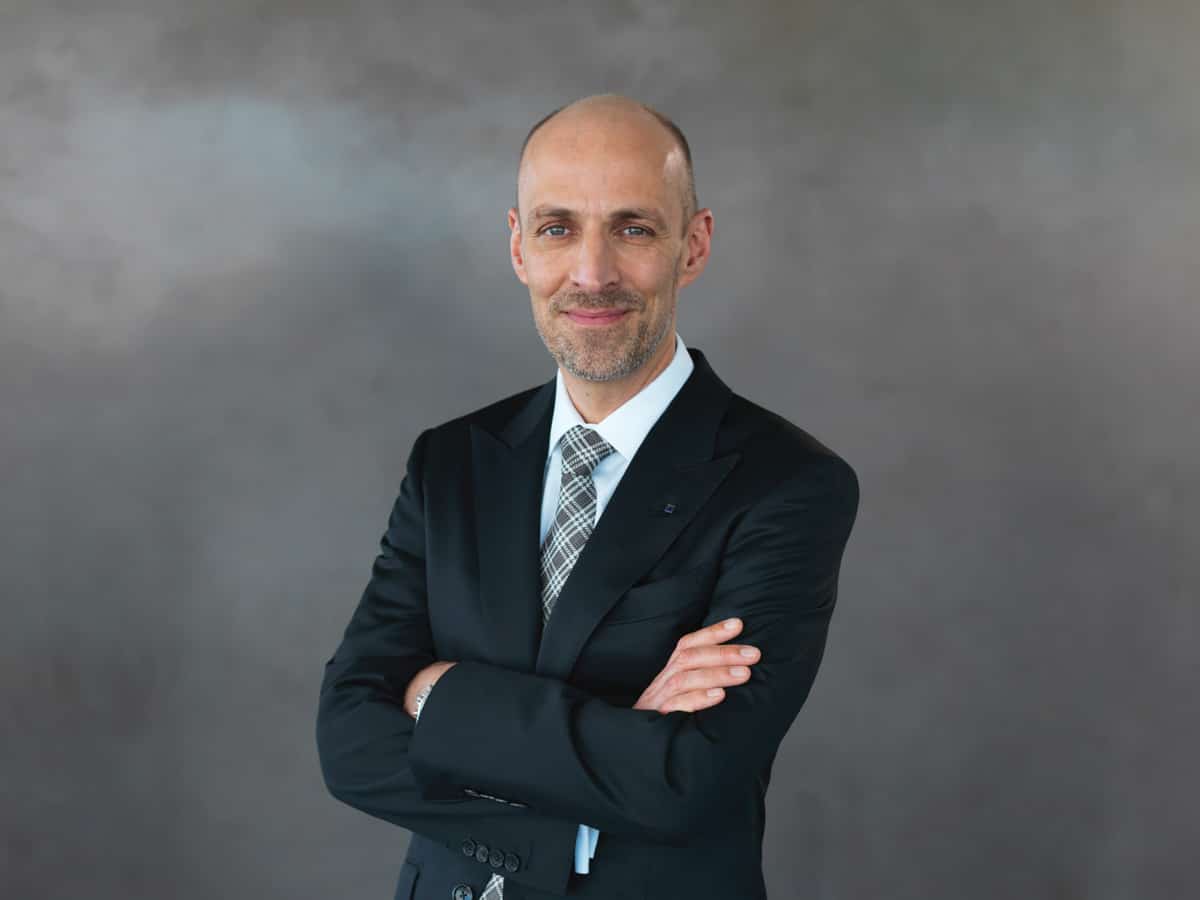
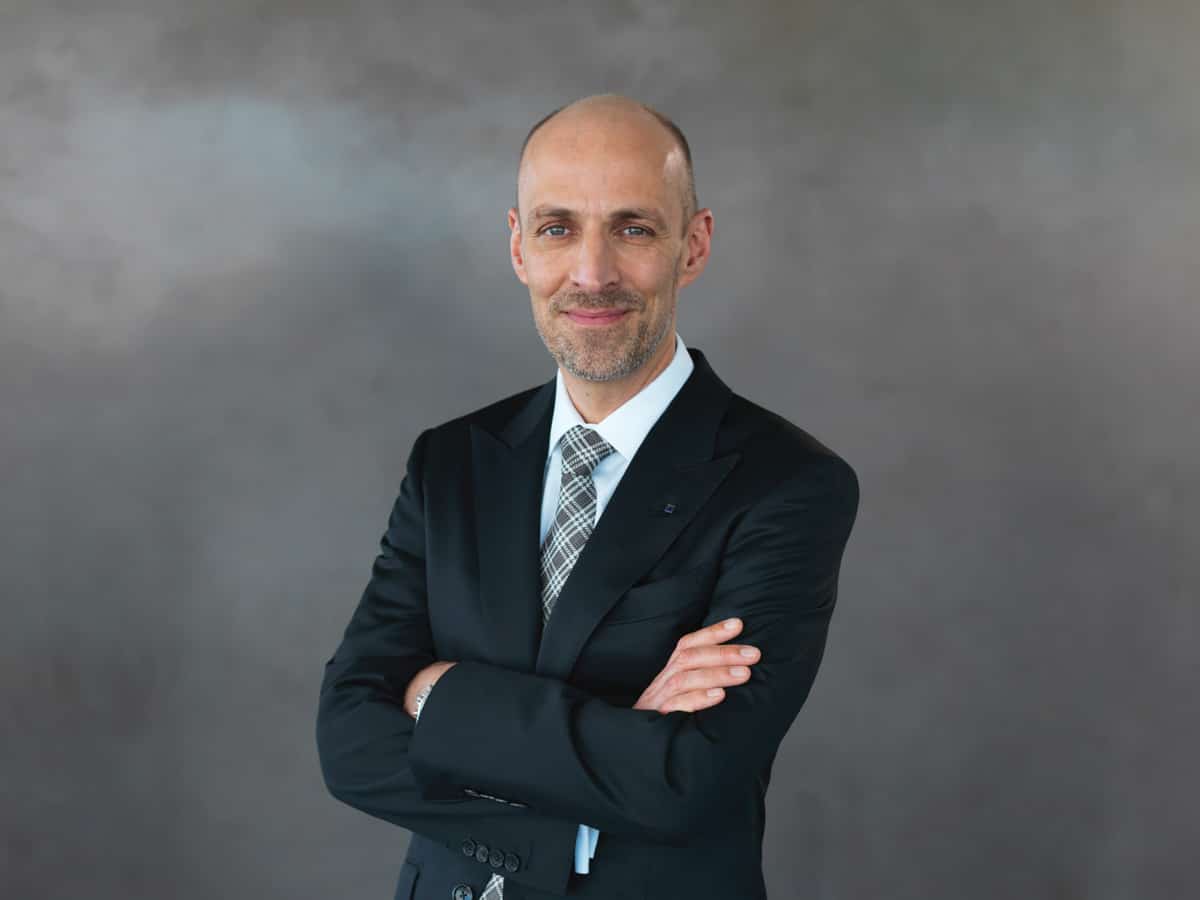
The team found that there is a well-defined boundary between stable and unstable keyholes. “You can think of the boundary as a speed limit, except it is the opposite of driving a car,” Rollett says. “In this case, it gets more dangerous as you go slower. If you’re below the speed limit, then you are almost certainly generating a defect.” However, he continues, “As long as you stay out the ‘danger zone’ (that is, too hot, too slow), the risk of leaving defects behind is quite small.”
The researchers, who report their work in Science, say they now plan to investigate ultrafast keyhole dynamics as well as other modes of instability in the laser melting process. “We also plan to study the development of microstructure from the rapid solidification and cooling inherent in LPBF additive manufacturing,” Rollett tells Physics World.
from physicsworld.com 17/12/2020
Δεν υπάρχουν σχόλια:
Δημοσίευση σχολίου