How a technique for recycling rare-earth permanent magnets could transform the green economy
James McKenzie looks at the work of University of Birmingham spin-off firm HyProMag, which has developed a technique for recycling rare-earth magnets

I recently went on a trade mission to Canada funded by Innovate UK, where I met Allan Walton – a materials scientist who co-founded a company called HyProMag. Spun off from the University of Birmingham in 2018, HyProMag has developed a technique for recycling rare-earth magnets, which are widely used in wind turbines, electric-vehicle (EV) motors and other parts of the “green economy”.
Having been invited to tour HyProMag’s prototype recycling facility on the Birmingham campus, I saw that the technology was shaping up to be a great UK success story. So when Physics World sent me a press release announcing that the company is due to start commercial production at Tyseley Energy Park in Birmingham by mid-2024, I knew my instincts were well founded.
Rare-earth permanent magnets – as I described in my column a few months ago – are alloys of elements such as neodymium, samarium and cerium. With the transition to a “clean-energy” economy now in full swing, demand for rare earths is high. Estimates suggest that the market will grow by as much as a factor of seven between 2021 and 2040.
Trouble is, some 80–90% of the world’s neodymium is currently made – or controlled by – Chinese companies. That’s prompted some nations, such as the US, to revamp their own production of permanent magnets. But another way to secure supplies of rare earths is to recycle materials. That’s why the imminent start-up of HyProMag’s facility is so interesting, especially as its process is so energy efficient.
Extracting elements
There are lots of possible methods to extract rare-earth elements from waste materials or from products that have reached the end of their lives. Most of the work has so far focussed on getting the individual elements by first dissolving the magnets and then recovering the rare earths from liquid-waste streams that re-enter the supply chain early in the magnet-making process.READ MORE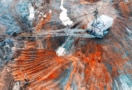
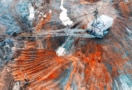
This approach is often called “long-loop” recycling as everything is broken down using various techniques and recovered as rare-earth oxides. These oxides then have to be converted into metals before being cast into alloys and broken down into a fine alloy powder to make the magnets. Long-loop recycling is an important but energy intensive and expensive process.
The Tyseley plant takes a different approach, based as it is on the University of Birmingham’s patented Hydrogen Processing of Magnet Scrap (HPMS) technique. It uses hydrogen as a processing gas to separate magnets from waste streams as a magnet alloy powder, which can be compactified into “sintered” rare-earth magnets. Not requiring heat, it’s a relatively quick process dubbed “short-loop” recycling.
A staggering 259 million hard disk drives were shipped in 2021, so the market for recycled magnets is huge.
When I looked around the company’s prototype line last year, I noticed that it can recycle the hard disk drives (HDDs) found in computers. Each disk can have as much as 16g of magnetic material, about a quarter of which are rare-earth elements. That’s only a small fraction of the disk’s overall mass but, as you’ll recall me pointing out, a staggering 259 million HDDs were shipped in 2021, so the market is huge.
HyProMag’s production method involves a robot with magnetic-field sensors first identifying the location of the HDD’s motor, which contains the all-important rare-earth permanent magnet. The section with the motor is then chopped off, with the rest of the disk sent for conventional recycling. The motor section is finally exposed to hydrogen at atmospheric pressure and room temperature via the HPMS technique.
Amazingly, the rare-earth magnets – typically alloys of neodymium, iron and boron (NdFeB) – just break apart to form a powder. I’ve seen videos of the process and it’s like watching something turn to rust. Crucially, the powder becomes demagnetized so any coatings on the magnet peel away from the surface of the magnets and can be easily separated.
The extracted NdFeB powder is then sieved to remove impurities before being re-processed into new magnetic materials or rare-earth alloys. HyProMag reckons that the process requires 88% less energy than that needed to make rare-earth magnets from primary sources, which is impressive. It has already produced more than 3000 new rare-earth magnets at its pilot plant for project partners and potential customers, with the magnets tested in a wide range of applications in the automotive, aerospace and electronics sectors.
Production promises
But the company wants to get past the trial phase and become a volume supplier of magnets. That’s why the Tyseley scale-up plant is so important. The company reckons it will initially be able to process up to 20 tonnes of rare-earth magnets and alloys a year – and eventually five times that amount. HyProMag is also planning further facilities in Germany and the US.
The technology is promising because so many products contain rare-earth magnets, but when they’re scrapped the magnets get shredded and break apart. The resulting powder remains magnetic, sticking to the ferrous scrap and plant components, but less than 1% of the magnets get recycled. HyProMag can, however, efficiently remove this material before it’s shredded and is already eyeing up a diverse range of economically viable sources of scrap.
“It is difficult to see large-scale recycling of rare-earth magnets taking off without an efficient separation process such as HPMS,” Walton says. “The current pilot line allows us to process up to two tonnes of scrap applications in a single run, with the commercial plant scaled to allow much larger batch sizes.” Loading to powder removal can be done, the company claims, in as little as four hours.
As the demand for rare earths increases and the amount of second-hand magnetic material available also rises, recycling such magnets is becoming an ever-bigger opportunity and an ever-more viable process. Just look at the growth of the EV sector: a typical electric motor has 2–5 kg of magnetic material and worldwide sales of EVs are expected to rise to 65 million per year by 2030, according to market-research firm IHS Markit.
Another huge source of rare earths are wind turbines, many of which are reaching the end of their lives after decades of use. Their generators contain up to 650 kg of rare earths per megawatt of generator capacity. Given that the UK aims to have up to 75 GW of off-shore wind capacity by 2050, it will have nearly 50,000 tonnes of rare-earth magnets in the years to come, according to Martyn Cherrington from Innovate UK, who runs its Circular Critical Materials Supply Chain (CLIMATES) programme.
Such long-term opportunities often need government support – and the recycling of rare-earth permanent magnets has been no exception. Indeed, the fundamental research behind HyProMag’s work began many years before it was spun off. The company has also benefited from financial support from a range of sources, including UK Research and Innovation’s Driving the Electric Revolution programme, the European Union and private investors.
In 2023 HyProMag Ltd was bought by the Canadian firm Maginito, which is part of Mkango Resources – a mineral-exploration and development company listed on the UK and Canadian stock exchanges. Mkango clearly saw the potential of HyProMag’s recycling and magnet-manufacturing technology. It’s a great UK success story, which could have huge long-term global potential for the circular economy.

James McKenzie is the writer of the Transactions column for Physics World about physics in industry. He is writing here in a personal capacity.
FROM PHYSICSWORLD.COM 2/4/2024
Δεν υπάρχουν σχόλια:
Δημοσίευση σχολίου