Cleaner vacuum environments deliver experimental and manufacturing gains
20 Dec 2022 Sponsored by ANCORP
A new partnership between ANCORP and LOS Vacuum Products will enable scientists and engineers to optimize the vacuum conditions for their processes by exploiting the properties of aluminium and titanium
Breaking the mould: this multiport cluster flange, which was purpose built for a physics experiment at ETH Zurich, has an aluminium base with flanges that are faced with titanium (Courtesy: LOS Vacuum Products)
As science and technology continues to break new boundaries, there is growing demand for cleaner and more controllable vacuum environments that can be tailored to the needs of each application. Whether for precise experiments in quantum physics or the mass manufacture of computer chips, scientists and engineers are looking for high-performance equipment that can achieve ultrahigh vacuum (UHV) or extreme high vacuum (XHV) conditions while also working within the constraints of their application.
While vacuum systems made from stainless steel continue to be the technology of choice for most processes, specialized applications that require UHV or XHV conditions can benefit from the properties offered by alternative materials such as aluminium and titanium. In research centres with particle accelerators, for example, aluminium has become popular for beamline systems because it dissipates radiation more efficiently than stainless steel. It also retains less residual magnetism, minimizing any possible influence on the strong magnetic fields used to steer the beam.
“More scientists and engineers are seeing the benefits of using aluminium and titanium for their UHV or XHV processes,” comments Tom Bogdan, vice-president for business development at ANCORP, a US-based manufacturer of vacuum chambers, valves and components. “Large-scale scientific facilities and the R&D community offer rich environments for these advanced technologies, while the commercial sector is also starting to use aluminium to improve the process conditions for high-precision manufacturing.”
Bimetal bond: The explosion bonding process forms a wave-shaped join between two metals that is capable of withstanding XHV conditions. (Courtesy: LOS Vacuum Products)
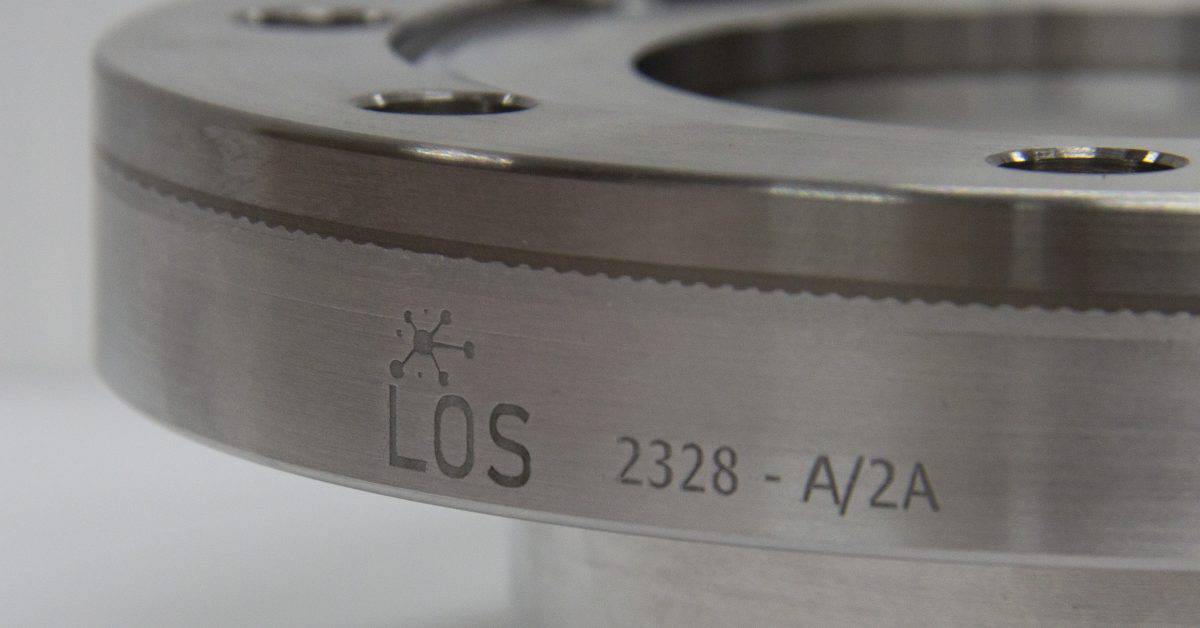
ANCORP designs and manufactures its own line of vacuum equipment, and has also established a dedicated facility for constructing customized chambers from stainless steel. Now the company has formed a partnership with LOS Vacuum Products, which specializes in fabricating vacuum hardware from aluminium and titanium, to enable its customers to exploit these high-performance materials in their UHV and XHV processes. “This is a great partnership between two companies who are focused on delivering high-performance vacuum solutions for their customers,” comments Bogdan. “LOS Vacuum will benefit from our ability to make connections with the global market, while we gain from adding their unique technology to our product portfolio.”
LOS Vacuum Products was set up in 2013 to design and build bespoke vacuum chambers for UHV and XHV applications. “Aluminium and titanium are becoming more popular to meet the growing requirements for cleaner and more precise technology development,” says Eric Jones, the company’s founder and owner. While the initial demand originated mostly from the research community, Jones reports growing interest from equipment manufacturers targeting the semiconductor sector, as well as emerging markets for medical systems and solar-cell production. “As those technologies grow the vacuum environment becomes critically important,” he says.
One key advantage of aluminium is that it is quicker and easier to machine than stainless steel, and so offers more flexibility for incorporating bespoke features into the design. Its superior thermal conductivity also allows an aluminium chamber to heat up faster and more uniformly, which speeds up the bake-out process needed to achieve UHV or XHV conditions. “Stainless steel needs to be much hotter to desorb the gas molecules and contaminants from the surface of the vacuum chamber, and that requires more energy over a longer period of time,” explains Jones. “Aluminium reduces both the cost-of-ownership and the environmental impact, which combined with its enhanced manufacturability makes it an attractive option for the semiconductor sector.”
Bespoke fabrication: This bimetal transition fitting, which combines stainless steel with aluminium has a diameter exceeding 60 cm. A range of bespoke components can be made to meet the needs of different applications. (Courtesy: LOS Vacuum Products)
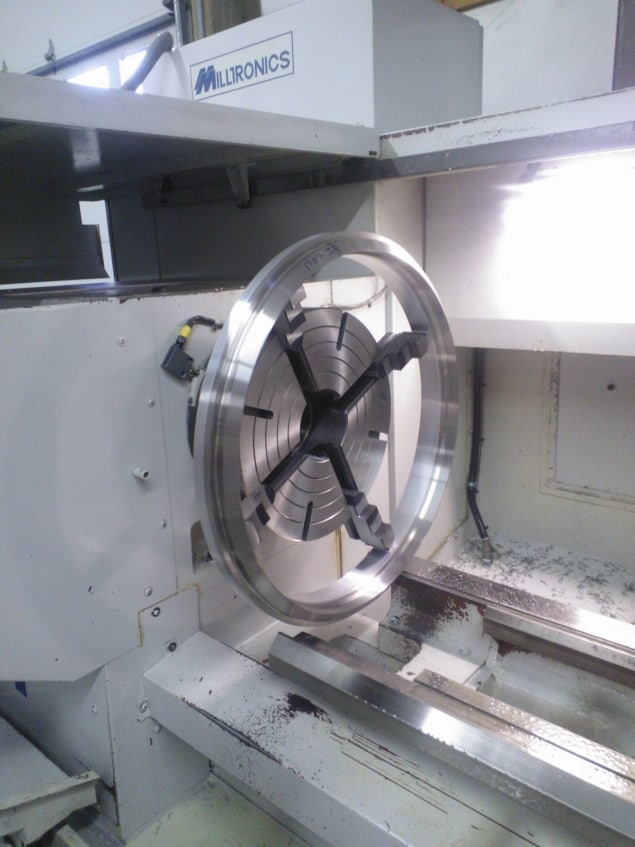
Meanwhile, vacuum chambers made from titanium offer a better option for experiments in quantum physics, since their extra strength and weight provide more stability for processes that benefit from the generation of harmonics, and are also favoured for applications where it is essential to eliminate any magnetic signals. Titanium also acts as a getter for absorbing hydrogen – a common contaminant when using stainless steel in UHV or XHV environments – which enables titanium vacuum systems to support XHV conditions down to around 10–13 Torr.
Whether using aluminium or titanium, the best process conditions are achieved by using the same metal in the fixtures and fittings used to interface with the vacuum system. That includes the conflat flanges that are widely used to ensure a leak-tight seal in UHV and XHV environments, which work by pressing two hard metal faces machined with knife edges into a softer metal gasket. This causes the softer metal to flow and fill any microscopic imperfections on the hard metal faces, creating a seal that can withstand extreme temperatures and pressures down to the XHV regime.
ANCORP already manufactures conflat flanges made entirely of stainless steel, while LOS Vacuum produces all-titanium versions as well as several models that combine an aluminium body with faces made of stainless steel or titanium. “The specialist components fabricated by LOS Vacuum allow us to offer a unique solution for customers who have adopted aluminium or titanium for their vacuum systems,” comments Bogdan. “We have seen customers who have resorted to using double O-rings for their enclosures, but a metal-to-metal seal reduces outgassing and results in a better process.”
The bimetal components are fabricated using a technique called explosion bonding, a solid-state welding process that produces a strong mechanical bond just a few microns thick. An explosive charge forces the metals together at extremely high pressures, causing the atomic layers close to the two surfaces to become a plasma. As the metals collide a jet of plasma is propelled along the surfaces that scrubs them clean of any impurities, while the fluid-like behaviour of the metals creates a wave-shaped join that is strong enough to withstand UHV and XHV conditions.
ANCORP now supplies a standard line of bimetal flanges and fittings produced by LOS Vacuum, while the explosion bonding process also enables bespoke components to be fabricated from any two dissimilar metals. Two of the standard configurations combine an aluminium base with faces made from different grades of stainless steel, while another joins a titanium-faced flange to an aluminium body. This second version has the advantage of eliminating any trace magnetism and avoiding the safety hazards caused by background radiation, and can even be more cost effective than a flange faced with stainless steel. “The raw material may be more expensive but a bimetal flange made from stainless steel requires more steps to fabricate,” comments Jones. “For titanium the bonding process is less complex and less expensive.”
Jones and his team have also been able to eliminate one of the interlayer materials that are usually needed to transition from one metal to another. Their process removes the need for copper, which semiconductor manufacturers are particularly keen to avoid. “That’s now part of the standard product line,” says Jones. “It cuts the cost of materials and manufacture, and reduces the possibility of a leak pathway through the flange.”
Added options: Products available from ANCORP through the partnership with LOS Vacuum include all-titanium vacuum chambers, bimetal face-gland fittings, and bimetal flanges. (Courtesy: LOS Vacuum Products)
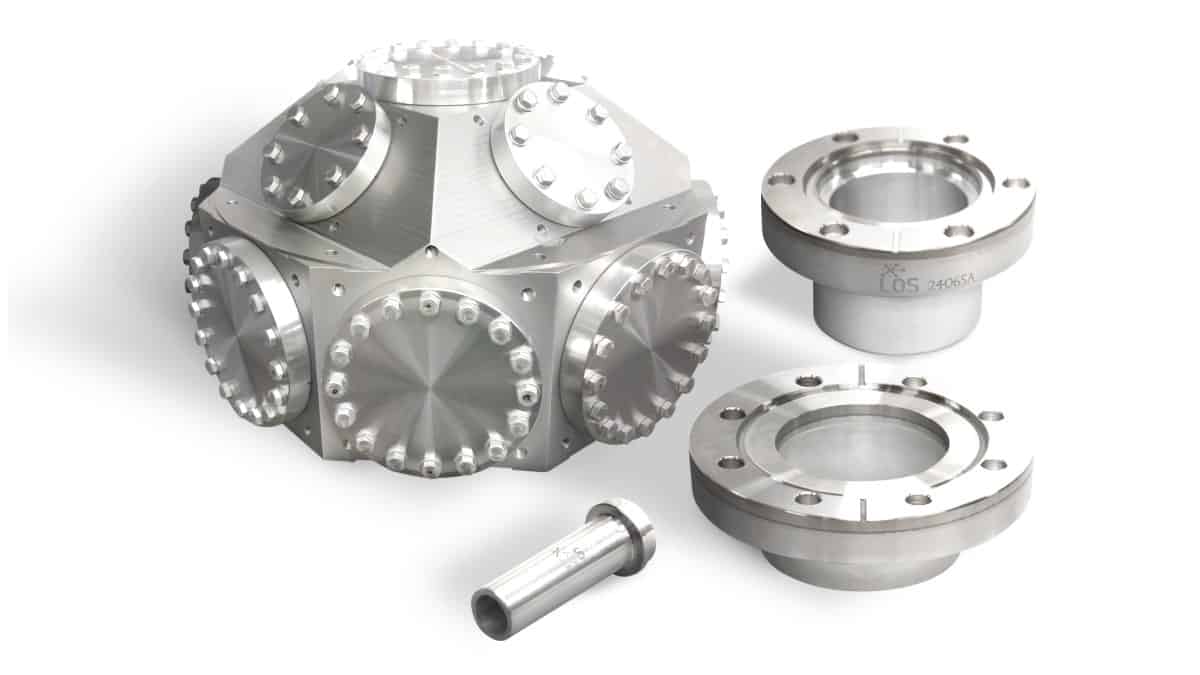
As part of the partnership ANCORP will also extend its existing custom fabrication capabilities to design and supply bespoke vacuum chambers made from titanium or aluminium. During the initial design phase the company works closely with its customers to understand their specific requirements and to recommend the best technology for their application. “If a customer has a particularly unusual or demanding process that would benefit from using aluminium or titanium, we’ll get Eric and his team involved to provide some specialist expertise,” says Bogdan. “As well as tailoring the design to the application, we need to ensure that the team at LOS Vacuum can manufacture the solution to the required parameters.”
Bogdan is confident that adding these specialized capabilities to ANCORP’s technology offering will help to open up new markets in the R&D sector as well as in semiconductor manufacture. “These low-outgassing solutions can deliver a real process advantage in some applications,” he says. “We want to make these options available to more customers in the international scientific community, as well as in the commercial sector.”
For Jones, meanwhile, the partnership with ANCORP offers a way to expose the company’s specialist fabrication techniques to a much larger customer base. “We’re still a small company that has focused on delivering unique solutions for specific projects, and we don’t have a lot of power for making connections with new customers,” he comments. “The partnership with ANCORP will enable us to bring our product range and technical expertise to the global market.”
Sponsored by ANCORP
from physicsworld.com 29/12/2022
Δεν υπάρχουν σχόλια:
Δημοσίευση σχολίου